LOS PROCESOS DE LA GESTION DE ALMACÉN
Los procesos de la gestión de almacén, representa el conjunto de las actividades bajo la responsabilidad de la gestión de almeces. En el, un primer proceso de planificación y organización de la función de los almacenes como subproceso inicial y que se extiende a lo largo de todo el proceso.
En un segundo nivel, los subprocesos que componen la gestión de las actividades y objetivos de los almacenes y que abarca la recepción de los materiales, su mantenimiento en el almacén y el movimiento dentro de un mismo almacén.
Y por ultimo, la gestión de las identificaciones, registro e informes generados a lo largo de los procesos anteriores.
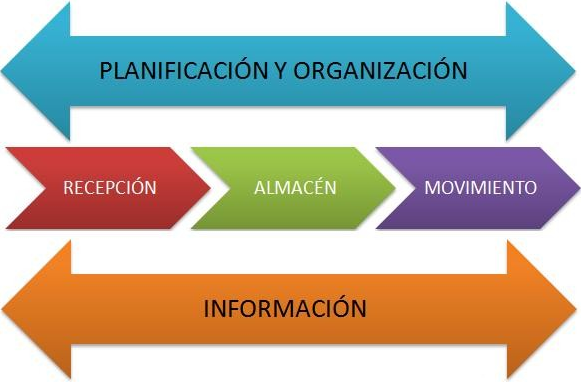
PLANIFICACIÓN Y ORGANIZACIÓN
El proceso de planificación y organización es de carácter estratégico y táctico, dado que tiene que brindar soluciones de recursos en comunión con las políticas y objetivos generales que contempla la estrategia de la empresa, para potenciar las ventajas competitivas por la que apuesta la misma. Dentro de las actividades o subprocesos que se deben realizar en el proceso de planificación y organización se encuentran:
- Diseño de la red de distribución de la compañía. Toda compañía necesita una red de distribución que permita responder a los cambios en la demanda utilizando una optima combinación de instalaciones, modalidades de transporte y estrategias. El diseño de una red de distribución es la planificación y ubicación estratégica de los almacenes y centros de distribución de manera que permitan gestionar el flujo de productos desde uno o varios orígenes al cliente. Desarrollar una adecuada red de almacenes para la compañía y los clientes, se requiere una cantidad significativa de elementos: numero de almacenes, ubicaciones, la propiedad de la gestión o tamaño de los mismos. Tras tener identificadas la necesidades de distribución y almacenaje, la compañía debe decidir que tipo de almacenes y centros de distribución se ajustan a sus necesidades y la ubicación de los mismos.
- Responsabilidades de la gestión de almacenes. Tras definir el diseño de la red de distribución por la compañía, la primera decisión que la compañía debe realizar respecto al almacenamiento de sus existencias es si debe autogestionar su propio almacén o subcontralalos. La decisión depende de muchos factores. En el siguiente cuadro se presenta las ventajas y desventajas de cada una de las modalidades, de manera que la empresa pueda decidirse por la que mejor le convenga.
La gestión propia del almacén ya sean de propiedad de la compañía o alquiler por un agente externo, es la propia empresa que lo gestiona. Por lo tanto la responsabilidad de las actividades que se realicen en el almacén, independientemente de quien sea la propiedad de las instalaciones.
La decisión respecto a la propiedad de las instalaciones responde únicamente a criterios financieros y es la propia empresa de tomar la alternativa mas ventajosa para si misma.
En casos de que la demanda tuvieran subidas temporales o que la previsión sea cambiante, podría la empresa aparte de tener su almacén propio, poder subcontratar almacenes para cubrir esos periodos de tiempo.
- Ubicación de almacenes. La localización de los almacenes debe ser enfocada desde los siguientes puntos.
- Una visión general del mercado para acotar geográficamente a un área amplia.
- Una visión local del mercado que contemple aspectos particulares de la zona acotadas en la visión general.
A lo largo de la historia se han desarrollado varios métodos matemáticos para la mejor localización del almacén desde el punto de vista general. Los métodos mas utilizado son: Von Tnünen, Hoover, Weber, Greenhut y el método centro de gravedad.
Los factores no son meramente cuantitativos y existen una gran numeros de criterios cualitativo, en el siguiente cuadro estan lo que mas destacan:
- Tamaño de los almacenes. El tamaño de los almacenes es un aspecto importante dentro de la planificación y organización de la gestión de almacenes, una mala decisión puede provocar graves problemas en los costes. El almacén debe ser dimensionados en función de los productos a almacenar (tamaño, características y cantidad) y la demanda (especialmente en sectores con demanda estacionaria). Ademas de estos factores, intervienen otros que hay que tener en cuenta, como:
- Productos a almacenar (cantidad y tamaños)
- La demanda del mercado
- Niveles servicio al cliente.
- Sistema de manipulación y almacenaje
- Tiempos de produccion
- Economías de escala.
- Lay out de existencias.
- Requisitos de pasillos.
- Oficinas.
- Diseño y lay out de los almacenes. Una vez se hayan definidos los tipos de almacenes y su ubicaciones, se debe trabajar en conseguir el flujo de materiales mas eficiente y efectivo dentro de los almacenes. En este sentido, un buen diseño optimiza las actividades dentro del almacén. Los riesgos achacables a las actividades del almacén son; se seguridad, de control de autorización, de control de inventarios, sanitarios, y manipulación de productos.
ALMACÉN
El almacenamiento o almacén es el subproceso operativo concerniente a la guarda y conservación de los productos con el mínimo riesgo para el producto, personas y compañías, optimizando el espacio físico del almacén. El almacén constan de las siguientes zonas:
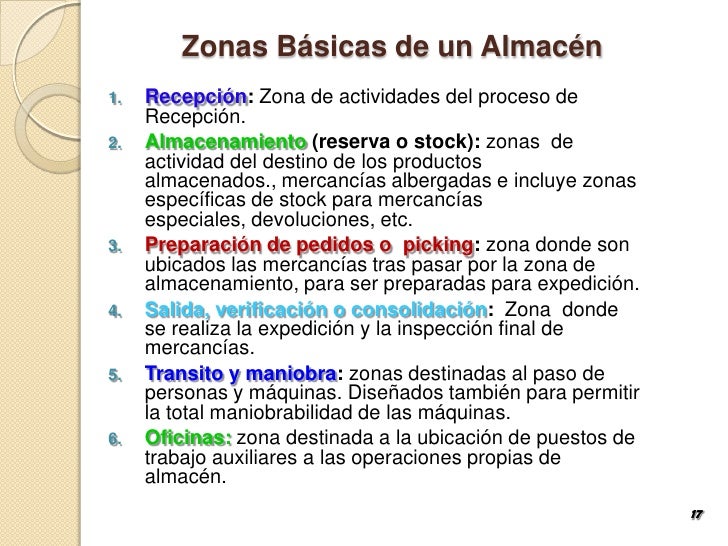
RECEPCIÓN
La recepción es el proceso de planificación de las entradas de mercancías, descargas y verificación tal y como se solicitaron actualizando los registros de inventarios.
El objetivo al que debe tener una empresa en su proceso de recepción de mercancías es la automatización tanto como sea posible para eliminar o minimizar la burocracia e intervenciones humanas que no añaden valor al producto. Otra tendencia considerada como una buen practica logística es la implementacion de programas de entregas certificadas que no solo elimina la burocracias sino también reducen las inspecciones que son imprescindibles pero que añadan valor.
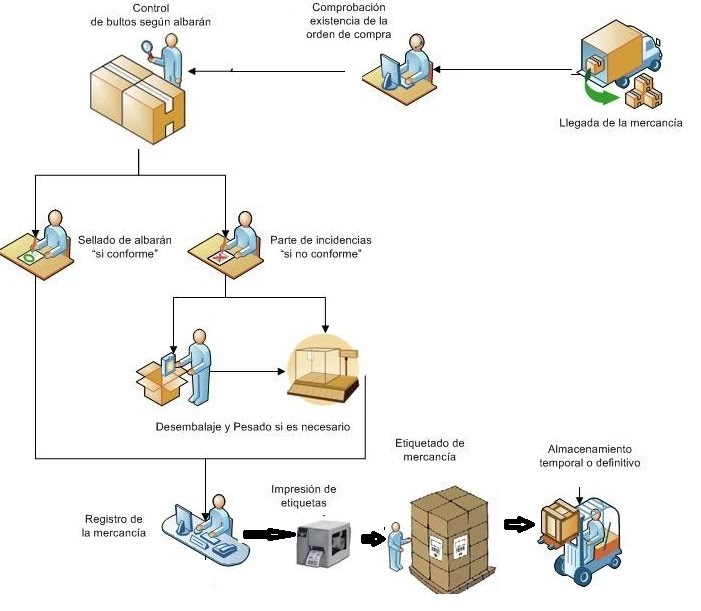
El proceso de recepción de mercancías debe cimentarse en una previsión de entradas que informe de las recepciones a realizar a tiempo dado que contenga, al menos, horario, artículos y procedencia de cada recepción, a este proceso se le denomina "cita previa".
Es importante que se distingan entre las llegadas internas y las externas. En el primer caso, los requerimientos de recepción son menores que las mercancías de origen externo, en el caso de que se realicen controles de procesos a lo largo de la vida de las mercancías. Ademas, una correcta metodología de identificaciones a lo largo de la compañía, favorece a la actividad de la recepción. Es el caso de traslado de mercancías entre almacenes o de proceso de transformación a almacén.
Las mercancías procedentes de entradas externas requieren unas condiciones de entradas mas exhaustivas y deben haber sido establecidas previamente con el proveedor, por lo que precisa una mayor actuación y responsabilidad desde el almacén.
Tras la descarga e identificación, las cuales deben realizarse de manera inmediata y en la zona habilitada a tal efecto, las mercancías deben pasar a almacenamiento, bien temporal a la espera de ubicación o bien con la ubicación definitiva.
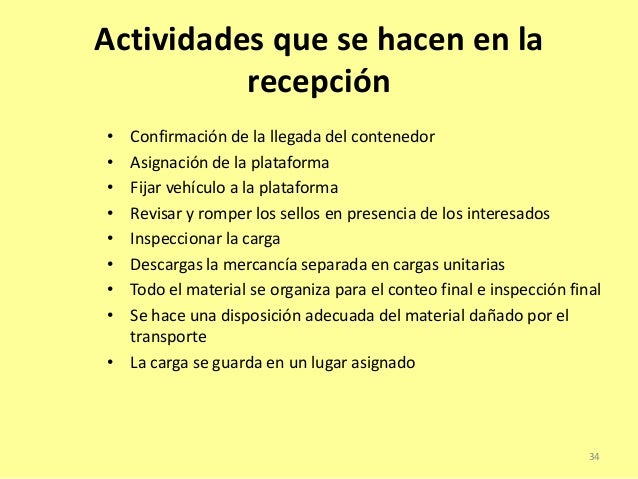
MOVIMIENTOS
Subproceso del almacén de carácter operativo relativo al traslado de materiales o productos de una zona a otra dentro de un mismo almacén o desde la zona de recepción a la ubicación del almacenamiento.La actividad de mover físicamente mercancías se puede lograr mediante diferentes medios, utilizando una gran variedad de equipos de manipulación de materiales. El tipo de herramientas que utilicemos depende de varios factores:
- Volumen del almacén
- Volumen de la mercancía.
- Vida de la mercancía.
- Coste del equipo frente a la finalidad
- Cantidad de manipulaciones especiales y expediciones requeridas.
- Distancia de los movimientos.
- Last In - Fisrt Out (LIFO): la ultima mercancía que entra en el almacén, es la primera que sale para una expedición. Normalmente utilizada para producto frescos.
- First In - First Out (FIFO): la primera mercancía que entra en el almacén, es la primera que sale del almacén. Es utilizadas para evitar obsolescencias.
- First Expired - First Out (FEFO): mercancías con fecha de caducidad mas próxima, es la primera que sale del almacén.
INFORMACIÓN
Si bien la función principal de gestión de almacenes es la eficiencia y efectividad en el flujo físico, su consecución esta a expensas del flujo de información. Debe ser su optimizacion, por tanto, objetivo de primer orden en gestión de almacenes.Su ámbito se extiende a todos los procesos anteriormente descritos: planificación y organización, recepción, almacén y movimiento, y se desarrolla de manera paralela a ellos por estas vías:
Información para la gestión. Dentro de este epígrafe se incluyen todos aquellos documentos que contiene:
- Configuración del almacén: instalaciones, lay-out...
- Datos relativos a los medios disponibles.
- Datos técnicos de la mercancía almacenada.
- Informes de actividad para Dirección.
- Evolución de indicadores
- Procedimientos e instrucciones de trabajo
- Perfiles y requisitos de los puestos.
- Registros de la actividad diaria.
Toda ubicación en el almacén debe tener su codificación diferente al resto. El método de codificación es decisión de la empresa, no existiendo una codificación perfecto para cada una de ellas. Cada empresa debe buscar la suya en función del numero de almacenes, las zonas de cada uno de ellos y la ubicaciones en cada zona.
Las ubicaciones pueden codificarse por:
- Estanterías. Cada estantería tiene asociado una codificación correlativa, del mismo modo que en cada una de ellas, sus bloques también están identificados con numeración correlativa, asi como la altura de la estantería, empezando en el nivel inferior y asignando numeración correlativa conforme se asciende.
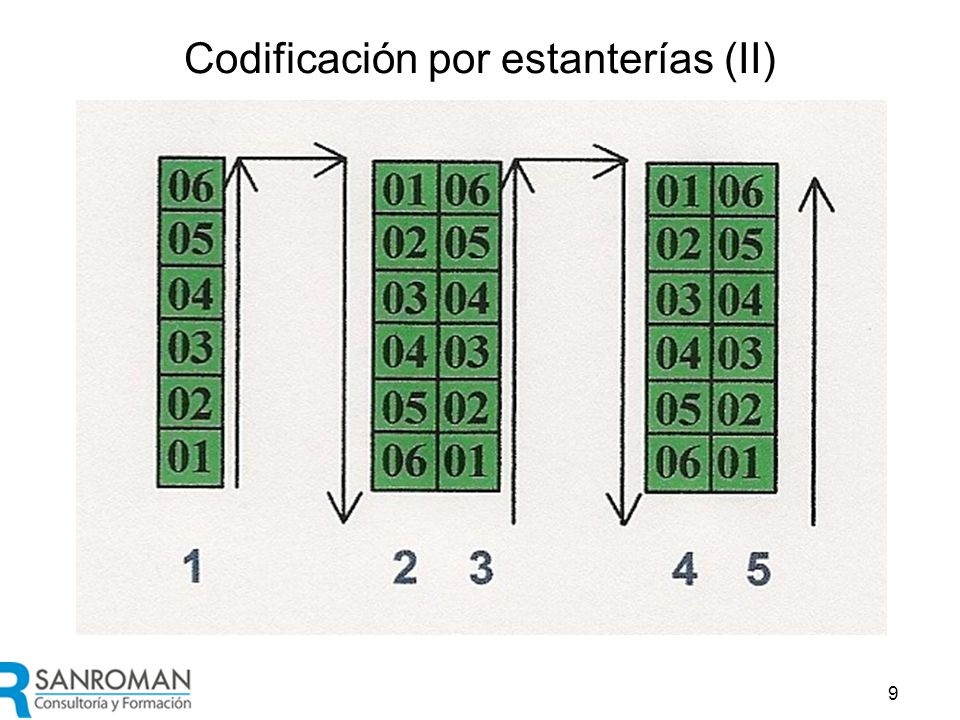
- Por pasillos. En este caso, son los pasillos que se codifican con números consecutivos. Cada dos estanterías se van codificando sus bloques, ya que la relación es de un pasillo para cada dos estanterías. La profundidad de la estantería se codifican con numeraciones de abajo arriba, y empezando por el lado opuesto del siguiente pasillo.
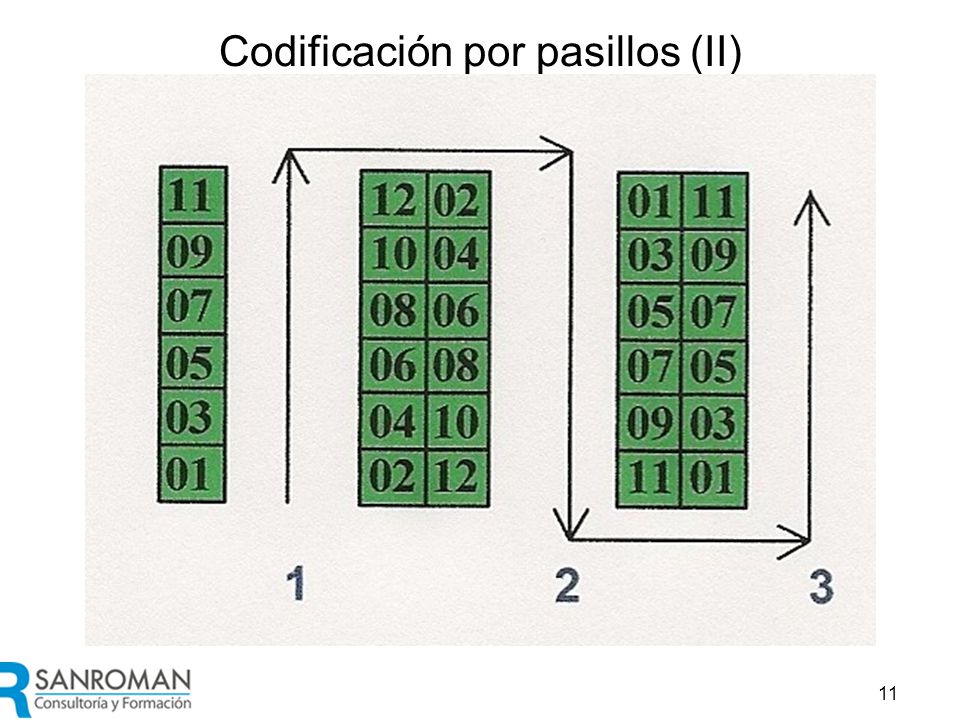
Las principales vías de codificación automática que se utiliza son:
- Codificación de barras. La gestión de almacenes basadas en código de barras permite un control exhaustivo de los productos. Es un sistema de codificación internacional de los productos que ofrece grandes posibilidades para maximizar la eficiencia en la gestión de las bases de datos que relaciona los flujos físicos y de información de las empresas en sus operaciones cotidianas de intercambio. El sistema EAN proporciona la formula para identificar de forma única y no ambigua a los artículos y productos, cualsea su formato o presentación. El código EAN dispone de un principio básico de gestión: "Toda modificación del producto percibida por el consumidor final tiene un código EAN distinto".

Ejemplo código de barras
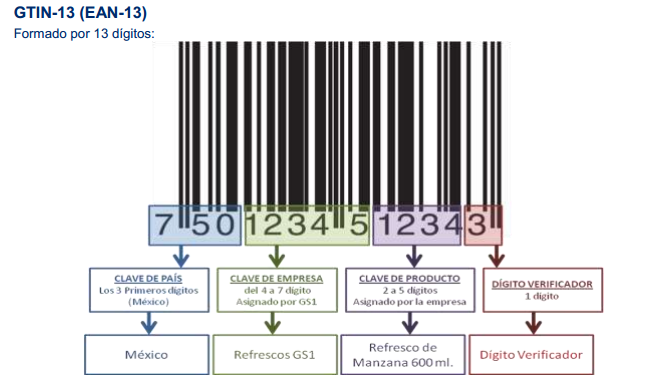
- Etiquetas electrónicas. Son un recurso mas sofisticado. Están basada en circuiteria con microprocesadores, receptores de radio, memorias y emisores, lo que les permiten manejar volúmenes de información de miles de bytes. Su penetración es sensiblemente inferior al código de barras.
No hay comentarios:
Publicar un comentario